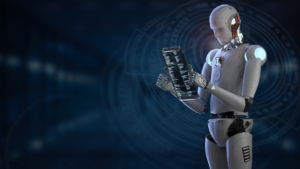
AI-Driven Application & Process Testing: Embracing Agentic Testing
Learn how Agentic AI enables digital transformation, delivering true hyperautomation.
Social, environmental, and economic drivers are accelerating the shift towards a circular economy, as described in this article. In the following article, we take a look at potential business models for players in the automotive industry in connection with the energy-storage life cycle.
The global need to reduce greenhouse gas (GHG) emissions and the growing need for individual and sustainable mobility are just a few examples of the phenomena that are creating challenges for the automotive industry. Due to these changes, automotive OEMs and tier-one suppliers are going to face a large transformation from the conventional combustion engine to other technologies to safeguard their businesses. One approach for overcoming these hurdles is to reduce the emissions of the powertrains used. Battery electric vehicles (BEV), fuel cells (FC), and power-to-gas are some popular technologies that could help to achieve this goal. This post provides an overview of current developments, with a particular focus on BEVs, and describes one of the biggest barriers for electric vehicles: the energy-storage life cycle.
Over the last decades, a number of measures became established to increase the efficiency of traditional vehicles with internal combustion engines (ICEs). However, the rate at which efficiency is increasing is flatlining more and more and there are no longer any expectations of major gains in powertrain development. Alongside this improvement, there has also been new legislation for ICEs and a demand to reduce GHG emissions, paving the way for new technologies to emerge in recent decades. Currently, there are three promising, noteworthy technologies that will significantly increase sustainability in private transport with passenger cars and in transportation and logistics with trucks and buses.
Hydrogen can be used in fuel cells as well as in power-to-gas engines. They offer a variety of technological benefits and some key OEMs such as BMW and Hyundai are investing in R&D and production facilities. Hyundai expects H2 fuel-cell vehicles to be on par with BEV prices in 2030. The potential that is being explored for power-to-gas is mainly in heavy-duty powertrain applications like trucks, buses, trains, planes, and ships, and not in the passenger-car industry. While there are some advantages in using fuel cells or power-to-gas engines based on hydrogen, a couple of (technological) barriers (e.g., the cost of producing the vehicle, technological maturity, cost of fuel, and profitability) need to be overcome. A detailed description of further barriers can be found in Trencher et. al. 2021 (pdf).
While the number of registered fuel-cell cars globally was in the tens of thousands in 2020, the number of registered BEVs is around 6,5 million. The large-scale production of batteries is being realized over the short and medium term, so this contribution will focus on BEVs. To meet the foreseeable rise in demand for batteries, several large battery manufacturing projects have been initiated in Europe, with a strong focus on Germany. Table 1 shows the production capacities for automotive batteries in early 2021.
Region | Countries | Energy [GWh] |
Germany | Germany | 312 GWh |
Eastern Europe | Poland, Slovakia, Hungary | 145 GWh |
Northern Europa | Norway, Sweden | 104 GWh |
Southwest Europe | Spain, France | 72 GWh |
UK | UK | 65 GWh |
Total | ~ 700 GWh |
Table 1: Overview of production capacities (extract from early 2021)
An overview of the different production sites and their location can be seen in Figure 1.
Customers in the automotive industry are used to widespread gas-station availability and fast refueling times. Therefore, the potential range and availability of rapidly charged energy is an important issue in making alternative powertrains successful. From a customer’s perspective, there are three major barriers that can be identified and that interfere with BEVs becoming competitive with ICE vehicles in the short term:
Although the complexity of a BEV powertrain is less in comparison to an ICE powertrain and key elements (e.g., the gearbox and gearshift) of an ICE are not necessary, the production of BEVs is still expensive today compared to combustion-engine vehicles. This mainly results from the costs of mining and processing the raw materials and the overall production costs for the energy’s storage. Since, relatively speaking, the cars’ interior and body stay the same, the focus is on gaining a competitive edge by producing affordable batteries with growing capacity and reducing emissions during the production stages for the final product and the materials required.
One way of reducing the overall GHG emissions of a powertrain during the utilization stage is by extending the battery’s lifetime. This in turn shifts the focus to the aftermarket and product maintainability. In comparison to ICE-powered vehicles, the BEV value chain is becoming more complex because there is a growing significance on reusing components and raw materials. In the past, old ICE cars were maintained and resold if possible, before being scrapped for low-value parts and resources. Right now, the market for used BEVs is only just starting to emerge. The resource value in BEV is significantly higher and harder to recover than with ICE vehicles. Consequently, the recycling requires special capabilities and significant effort and prolongs the value chain. The recyclability of BEV components is therefore an important feature to take into consideration. In the BEV aftersales market, there is huge potential for adding value and unlocking new market segments while increasing the industry’s overall sustainability significantly. A shift from ICE components to more-complex battery systems is a challenge for the current aftermarket structure and capabilities. [1]
Due to the rising demand for BEVs, there will be many batteries coming to the end of their (first) life in the next decade and, by extension, coming to the market with significantly reduced power/productivity. Because the technology is at a relatively early stage of its maturity curve compared to ICEs, there are few approaches available to prolong the life of components, recycle the elements within batteries, or even just prevent complete disposal. The “waste-hierarchy pyramid” offers an approach for better understanding the effects of waste prevention and measures that prolong the life of products and parts.
The waste-hierarchy pyramid is a concept that describes the hierarchy for handling waste. Seen from top to bottom, the current overall waste volume increases, whereas the impact of sustainability measures grows considerably the further up the hierarchy they go. Figure 2 shows the levels of the waste-hierarchy pyramid and describes typical strategies for waste prevention and the estimated waste volume.Waste Hierarchy Pyramid
The waste pyramid is a concept which describes the hierarchy of how to handle waste. From top to bottom, the current overall waste volume increases while the impact of sustainability measures grows extensively when they are implemented higher up the hierarchy. Figure 2 shows stages of the waste hierarchy pyramid and describes typical strategies for waste prevention and the estimated waste volume.
Each level of the waste hierarchy describes how the waste is dealt with. The following describes the levels of the waste-hierarchy pyramid:
At the top level, the goal is to reuse a product for as long as possible and not to require new products. Measures aim at sharing, maintaining, and even repurposing products to extend their life cycle. Some OEMs set strategies for maintaining their batteries. Daimler, for instance, guarantees an 80% state of health (SOH) for eight years. Strategies for giving batteries a second life consist of home and industrial storages of self-produced renewable energy.
Products that no longer work sufficiently are repaired or fitted with replaced parts to prolong the life of the core product. The remanufactured product reenters the same market as the original product. When looking at ICEs as they are used in vehicles, a few of their parts, such as clutches, starters, or gearboxes can be remanufactured [3]. Many of these parts are not relevant for BEVs. The current discussion surrounding sustainability for BEVs involves battery cells, battery packs, or battery casings being recovered and remanufactured as one major component of BEVs, alongside the engine and electrical circuit.
This refers to recovering the raw material to produce new products. As the volumes are still low, the current recycling processes are complex and often energy-intensive. Nevertheless, recycling is necessary since resources are rare and mining also has a vast impact on emissions. When it comes to electronical components, the rare earths and significant amounts of lithium in batteries are the focus of recycling efforts.
If a product’s material cannot be transformed into a reusable state, incineration often becomes a measure of last resort in order to at least recover energy from the products.
Waste that cannot or should not be burned is disposed of in landfills around the globe, often in an unregulated manner.
A study of the current aftermarket for automotive batteries has identified a focus on recycling and/or remanufacturing batteries. To achieve this, “battery alliances” have often been formed to address different developments in relation to extending battery-cell life, recycling battery cells, or remanufacturing them. The Global Battery Alliance, counting 70 members (such as BMW, Honda, BASF, and Google), wishes to develop a circular-economy approach for BEVs. Meanwhile, the main goal of the Automotive Cells Company (ACC), featuring Daimler, Saft, and Stellantis, wants to increase BEV recyclability to up to 95% in order to extend their life span. The Battery Value Chain Collaboration focuses mainly on closed-loop recycling of EV-battery metals. These are just three famous examples of OEMs, suppliers, and traditional recyclers pooling their knowledge. In addition to the battery alliances, some OEMs and suppliers are also implementing their own approach to recycling or remanufacturing the batteries. Tesla is an example of this latter approach.
With regard to the waste-hierarchy pyramid, one idea is to turn the volumes in the pyramid upside down to obtain more value out of the higher stages of the pyramid. There therefore needs to be a consideration of technologies that focus on reusing or remanufacturing batteries in order to add value. Figure 3 illustrates the inverted pyramid described here and the potential value added at different stages.
The reuse/second life of batteries outside a BEV is a promising way to generate profits. Due to the high technical requirements imposed on vehicle batteries in relation to their possible charging and discharging currents and their capacity, batteries can only be used in one vehicle for a limited time. Typically, they reach their end of life (EOL) at an SOH of 80% (typically referring to the first life). However, there are several applications where theses batteries can be used after they have passed this mark. One example is use within home battery storage for energy from solar systems or other renewable energy sources. Another example is to use several batteries for energy storage within businesses to allow more-flexible reactions to volatile energy prices. During periods of high energy prices, such storage can be used as a buffer for demand from production. New business models can be developed based on these applications to manage the different battery life cycles. Scientific studies forecast an available range of 112 to 275 GWh per year by 2030. [4]
Battery cells age unevenly and a single defect battery cell affects an entire battery’s SOH. [5] Minor defects may lead to inoperability for BEVs even if they still offer potentially high value. If reuse or a second life is not an option for a battery, remanufacturing battery packs promises high value-adding potential in comparison to recycling or burning. The typical use cases are replacing insufficient battery cells or modules or even other parts in the battery. Keeping these highly engineered products in use significantly increases value for customers. Accordingly, finding strategies for remanufacturing will be a key goal for the near future, offering great potential for the automotive industry and automotive suppliers.
We would like to thank David Dickmann and Julian Keens for their contribution to this article.
Read our further articles on this topic:
[1] D. Parker et al. 2015, Remanufacturing Market Study
[2] United Nations Environmental Program 2013. Guidelines for National Waste Management Strategies Moving from Challenges to Opportunities
[3] D. Parker et al. 2015, Remanufacturing Market Study
[4] The Second-Life of Used EV Batteries – Union of Concerned Scientists (ucsusa.org)
[5] Shi et al. 2017 Life prediction of large lithium-ion battery packs with active and passive balancing | IEEE Conference Publication | IEEE Xplore
Learn how Agentic AI enables digital transformation, delivering true hyperautomation.
Reimagine resilience and proactively minimize supply chain risks
This article shall help you to understand how to optimize your inventory positions in a month – or even less.
Modern PLM systems empower businesses to achieve product excellence in fast-paced markets by enhancing collaboration, agility and innovation.
© Camelot Management Consultants, Part of Accenture
Camelot Management Consultants is the brand name through which the member firms Camelot Management Consultants GmbH, Camelot ITLab GmbH and their local subsidiaries operate and deliver their services.