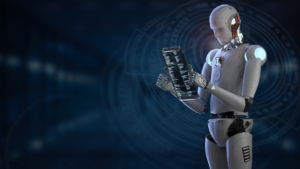
AI-Driven Application & Process Testing: Embracing Agentic Testing
Learn how Agentic AI enables digital transformation, delivering true hyperautomation.
Various developments point in the same direction for the German and European chemical industry: There is increasing pressure to source basic chemicals from renewable sources. This blog uses the example of renewable methanol production to show what is behind the trend, how mature the plans are, and what companies should consider when making the switch.
On an almost weekly basis, we receive news about newly planned infrastructure projects or strategic partnerships with which German and European chemical companies address not only their security of supply but also sustainability efforts in politically turbulent times. Many of these projects and alliances are directly or indirectly related to the hydrogen economy and basic chemical products derived from it, such as green ammonia or green methanol. But what is behind these trends, and why are they experiencing such a boost right now in times of great political instability and high energy prices?
As Germany’s second largest emitter of greenhouse gases in the manufacturing sector, the chemical industry is responsible for annual emissions of around 33 million metric tons (t) of CO2 equivalents.[1] Consequently, it faces the enormous challenge of having to reduce these emissions in the short term dramatically in order to meet the climate targets formulated by the European Union and the Federal Republic of Germany.[2],[3] Major chemical producers have proactively set ambitious targets, some of which even exceed the targets and timetables of the Federal Republic of Germany and the EU.[4],[5],[6] At the same time, the chemical industry will be forced to emancipate itself from Russia and China in terms of raw materials and to diversify.
In particular, it will be necessary to reduce dependence on Russian natural gas:
The political situation following Russia’s attack on Ukraine is accelerating the move away from fossil feedstocks, which was already foreshadowed by social pressure to operate more sustainably. Alternatives for supply must be found in order to reduce dependence. This is the only way to minimize future risks.
At the same time, these effects shorten the window of opportunity for companies to make decisions about the strategic direction of their radically changed supply chain and about significant investments in their infrastructure. If chemical companies want to achieve their economic as well as ecological goals, decisions must be made by the middle of this decade at the latest so that the subsequent implementation of the measures does not exceed the targeted time horizon.
In addition to the provision of heat and electricity from renewable sources, the switch from fossil raw materials and a mostly linear value chain to alternative raw materials from a circular value chain is a key leverage point for the transformation of the chemical industry. Being a classic B2B business, this conversion affects not only the chemical industry but also the numerous downstream industries that are also pursuing ambitious sustainability goals and must also meet these goals promptly due to legislative requirements. A lower-emission product range is, therefore, not an end in itself for achieving climate targets, but also an important differentiating feature in future competition and a way of minimizing risk in politically uncertain times.
The product range from the chemical value chain can be imagined as a tree with many branches: A myriad of different products in the crown can be traced back to a handful of basic chemicals in the trunk (Figure 2). A targeted change at the root or trunk accordingly influences a wide range of products for end consumers. It is, therefore, not surprising that the chemical industry focuses on a number of basic chemicals whose conversion from fossil to renewable sources is essential.[7] Therefore, in the next step, we explain crucial parameters by using methanol production as an example.
Methanol is one of the central building blocks in the chemical industry and is still mainly produced from natural gas on a large industrial scale in Europe. In Germany, in addition to production from natural gas, around 60% of methanol is currently still produced from heavy oil at the Leuna methanol plant.7 Nowadays, however, the classical means of methanol synthesis are contrasted by new, more sustainable synthesis means. These either use fossil feedstocks and avoid the release of CO2 from the process or alternatively use biomass or CO2 as a carbon source in combination with hydrogen. The products of these processes are more climate-friendly alternatives and are called blue and green methanol. In contrast to the established fossil synthesis processes scaled to a large industrial scale, these alternatives are currently still in a development or transition phase where they have yet to prove economic viability at comparable scales.
Pilot plants, such as BASF’s combination of alternative synthesis gas production and a methane pyrolysis plant in Ludwigshafen,[1] DOW’s Green MeOH project in Stade,[2] and Total’s e-CO2Met project in Leuna[3] are the first concrete attempts to scale these technologies in Germany. In addition, there are projects such as production in the Westküste 100 project and larger European projects in Denmark and Sweden.10,[4],[5],[6]
For the German pilot plants, initial production volumes of 500 t of methanol over three years are targeted in Leuna and up to 42,000 t per year in Stade.10 As a comparison: The current annual production volume at the Leuna refinery is about 700,000 t.[1] However, since a switch to alternative synthesis routes is inevitable in view of the political and climate circumstances, this discrepancy will have to shrink considerably in the near future. Instead of concentrating on fossil “world-scale” plants, methanol production will, therefore, temporarily become more fragmented and distributed among several smaller plants and different technologies before a renewed consolidation process occurs in the distant future. The blue or green methanol synthesized in these smaller plants will also be more expensive than the fossil alternatives for the time being, but according to forecasts, it will continue to converge in price until 2050.7 However, a significant increase in the price of fossil feedstocks, as is currently the case in the Ukraine crisis, could significantly accelerate this convergence process.
In the current extremely volatile environment, it is all even more important to set the course early on in order to be able to react adequately to the new reality. Companies that synthesize methanol or whose value chains rely on methanol should anticipate the changing supply structure early and take action to deal with a fragmented supplier environment, potential quality and specification differences, and more volatile price differentials between the various means of synthesis. The following aspects need to be considered:
There should be a comprehensive picture of available technologies and players along the methanol value chain.
Opportunities and risks of an emerging availability of methanol from sustainable sources for my company should be evaluated, and appropriate measures should be defined to exploit or minimize them.
Companies’ supply chains should be prepared as well as possible for a future scenario in which sustainably produced methanol will be available from regional plants in Europe as well as larger imports from sunny regions such as Australia and the Middle East.
The opportunities to reduce one’s environmental footprint through the production or incorporation of sustainably produced methanol should be quantified and set against the economic aspects.
Our conclusion: The chemical industry is under enormous pressure to change. Technological advances combined with societal pressures, political instability, and high feedstock prices are accelerating the shift from the production and distribution of fossil-derived methanol to methanol from renewable sources. This change will not have an isolated effect on the chemical companies themselves but also on customer industries such as marine logistics. Companies in the chemical industry are now faced with the task of assessing the impact of the change on their own business models and preparing changes strategically.
[1] VCI, “For greenhouse-gas-neutral chemistry”; 2020
[2] European Commission, “EU Green Deal”; 2019
[3] German Federal Ministry for Economic Affairs and Climate Action, “German Climate Protection Policy: Binding climate protection by the German Federal Climate Protection Act”; 2021
[4] Lanxess, “LANXESS to become climate neutral by 2040”; 2019
[5] Bayer, “How we protect the climate”; 2022
[6] BASF, “Our climate protection goal”; 2022
[7] VCI, Dechema, “Chemistry Roadmap 2050: On the way to a greenhouse-gas-neutral chemical industry in Germany”; 2019
[8] Adapted from the chart by VCI: “Basic chemicals production 2030”; 2012
[9] BASF, “BASF develops process for climate-friendly methanol”; 2019
[10] German Federal Ministry for Economic Affairs and Climate Action, “Winners of the ideas competition ‘Living labs of the energy translation’ -Profiles-” 2021
[11] Fraunhofer IGB, “TotalEnergies, Sunfire and Fraunhofer give the go-ahead for green methanol in Leuna”; 2021
[15] Adapted from the chart by IRENA: “Innovation Outlook: Renewable Methanol”; 2021
Learn how Agentic AI enables digital transformation, delivering true hyperautomation.
Reimagine resilience and proactively minimize supply chain risks
This article shall help you to understand how to optimize your inventory positions in a month – or even less.
Modern PLM systems empower businesses to achieve product excellence in fast-paced markets by enhancing collaboration, agility and innovation.
© Camelot Management Consultants, Part of Accenture
Camelot Management Consultants is the brand name through which the member firms Camelot Management Consultants GmbH, Camelot ITLab GmbH and their local subsidiaries operate and deliver their services.