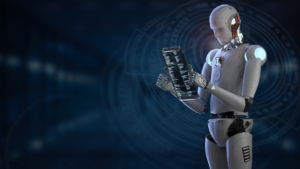
AI-Driven Application & Process Testing: Embracing Agentic Testing
Learn how Agentic AI enables digital transformation, delivering true hyperautomation.
This article focuses on remanufacturing as a key element of a circular economy. The first section explains the term “remanufacturing” more precisely. Then we focus on the added value for the customer, as well as for the producers of the remanufactured product. We discuss the necessary prerequisites for the successful implementation of remanufacturing within the company before we move to an illustration of the entire process in the last section, using electric vehicle batteries as an example.
Remanufacturing is a process of extensive refurbishing used, but usually not defective, products to restore them to the quality standards of a new product. To this end, the product in most cases is partially or completely disassembled in order to inspect the components and/or sub-assemblies. The product could possibly undergo technological upgrading if defective components need replacing. As a rule, remanufacturing is used to extend service life, for example in wind turbines. Remanufacturing is different from repair, reuse or refurbishing:
What all strategies have in common is that they help to prevent waste and to conserve primary resources.
Remanufacturing offers advantages and adds value on both the customer’s and the manufacturer’s side.
The prerequisites for successfully establishing remanufacturing in a company are explained below.
Efficient remanufacturing is based on three key elements:
In order to successfully implement the three key elements described, each potential component or product must be examined in its specific context. This means: Dedicated consideration must be given to materials, specifications, manufacturing methods, the market, the life cycle, the supply chain, and customer requirements, as well as the technical background. Based on the results of this, a remanufacturing strategy and roadmap can be derived for suitable products.
It is usually helpful to determine the status quo, as a baseline for a comparison with the perceived goal. This can be achieved with a remanufacturing maturity analysis as shown in figure 2. The maturity analysis is divided into an information phase and an evaluation phase. In the first phase, input for the assessment is gathered via interviews, line walks and process performance data. Subsequently, a multi-dimensional analysis evaluates the maturity level of the company with regard to the remanufacturing process. The production process, intralogistics, needed IT systems and supply chain planning processes are among the dimensions that must be evaluated. All dimensions count towards the above-mentioned key elements (product, reverse supply chain and business model).
Electric vehicle batteries are very well suited for consideration in the context of remanufacturing because the demand for these batteries will continue to grow in the coming years due to limited quantities of raw materials and rising raw materials prices. Also, the volume of used batteries will increase, providing more input for the remanufacturing process. Subsidies, such as e.g., the recently extended purchase premium for electric cars in Germany serve to further strengthen this trend. Figure 3 illustrates the requirements and the expected returns.
The expansion in remanufacturing electric vehicle batteries will lead to a drop in the production cost per KWh for batteries. For those active in battery remanufacturing, this will result in an increasing margin, or the opportunity to generate market share thanks to lower prices.
To evaluate the remanufacturing potential of battery cells, and to be able to design the necessary process appropriately, one needs to understand the building principles of the most common types of vehicle batteries:
The majority of electric vehicles are currently equipped with a battery that contains a battery pack consisting of several battery modules; called the cell module pack. The battery modules themselves are assembled from several battery cells connected in series (see figure 4 top row, cell module pack). Combining them into battery modules delivers a high battery safety. This is why this design is currently used as standard, even if the possible energy density is lower than in other building patterns.
With the second discussed building principle, the cell-to-pack technology, large individual cells are used, which are directly interconnected to form a battery pack (see figure 4, middle row). The advantage of this still fairly new design is that the energy density can be increased by 10 to 15 percent.
In order to achieve even higher energy densities than this, the brand new cell-to-chassis technology is currently being promoted (see. Fig. 4, bottom row). Here, the battery pack is directly integrated into the vehicle chassis. In terms of remanufacturing, we assume that this design will increase disassembly-related challenges.
Figure 4 illustrates the construction methods described above schematically.
In the following, we focus on remanufacturing processes for the first two variants. Rationale: Currently, cell-to-chassis design has not yet fully reached series production, and standard design and cell-to-pack strategy account for around 99% of the market.
For both construction methods under consideration, the remanufacturing process can be broken down into six main steps.
The described process is illustrated schematically in Figure 5:
The process is based on certain prerequisites for successful implementation. These relate to the required know-how in the company (overall company and personnel) as well as the necessary infrastructure for delivery, storage, testing and remanufacturing.
The know-how can be broken down into two sub-categories:
In addition to building know-how, the infrastructural requirements must be created to handle the cells and ensure a seamless remanufacturing process. These include:
These prerequisites are core requirements.
The article explains the remanufacturing process of technical products using the example of electric vehicle batteries. To this end, we provided an outline on the added value for customers and producers, discussed the core process of remanufacturing, and described the necessary prerequisites in terms of know-how and infrastructure. Based on the content presented, interested parties can implement initial steps to identify remanufacturing potential in the company (e. g. identifying relevant products).
Read our further articles on this topic:
[1] Zhao et al. 2021 – A Review on Battery Market Trends, Second-Life, Reuse and Recycling
[2] Kampker et al. 2020 – Battery pack remanufacturing process up to cell level with sorting and repurposing of battery cells
[3] Statista
[4] Second life or recycling? BattMAN rescues batteries from a needlessly short lifespan
[5] Steinhilper & Weiland 2015 – Exploring New Horizons for Remanufacturing – An up-to-date Overview of Industries, Products and Technologies
Learn how Agentic AI enables digital transformation, delivering true hyperautomation.
Reimagine resilience and proactively minimize supply chain risks
This article shall help you to understand how to optimize your inventory positions in a month – or even less.
Modern PLM systems empower businesses to achieve product excellence in fast-paced markets by enhancing collaboration, agility and innovation.
© Camelot Management Consultants, Part of Accenture
Camelot Management Consultants is the brand name through which the member firms Camelot Management Consultants GmbH, Camelot ITLab GmbH and their local subsidiaries operate and deliver their services.