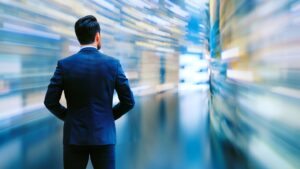
Product Excellence Through Modern PLM in Fast-Paced Markets
Modern PLM systems empower businesses to achieve product excellence in fast-paced markets by enhancing collaboration, agility and innovation.
The speed of technological development is increasing and so are changes in market behavior. Products or services which are relevant today are not necessarily relevant tomorrow. The cycles, companies need to consider when convincing customers of their offerings are getting shorter. Thus, a company constantly needs to adopt its portfolio and challenge it with requirements from customer and market inputs. This has driven the fast development of new product variants in the past years, which is likely to increase further. To compete in the market, manufacturers face the challenge of managing the increased amount of offered product variants accompanied by a growing product complexity. But how to solve this puzzle and mangage variant-driven supply chains?
The need for introducing different product variants can have various reasons. On the one hand, there are increasing customer expectations for individual products due to personal preferences. These can be related to individual tastes towards the product characteristics (e.g., color, flavor, design, size, etc.) or to personal circumstances (buy or rent options, prices, ethical attitude). On the other hand, variants might be needed for market entries due to regional requirements as for example language, plug types for electronic devices, regulations like labeling or FDA requirements, and weather conditions that require different material resistances.
While a broad product portfolio can serve and ensure customer satisfaction and offer new market opportunities, it simultaneously increases supply chain complexity. The strongly connected supply chain processes become harder to manage and tend to get inefficient. As a result, the related expenses for planning and execution increase as well.
We see five major pain points that drive complexity in product variant-driven supply chains:
A higher product variety makes accurate forecasting harder. The demand for specific variants can be very unstable or even unknown, especially if the variants are substitutable. Forecasts for newly introduced variants are usually just as unreliable. Thus, it is difficult for businesses to align demand and supply, respectively plan and replenish inventory.
Components are purchased on the basis of an unreliable forecast after bill of materials explosion in the MRP. Procurement needs to purchase the large variety of different components and materials which results in a higher effort in supplier management. It is hard to manage having the right components available to satisfy a specific customer order. Consequently, manufacturers are forced to offer their customers products with long lead times.
The higher the amount of product variants with unpredictable and fragmented demands, the higher the overall stock levels. Service level targets are often hard to achieve, and sales departments push for increased inventory levels to overcome the risk of potential stock outs. An increasing net working capital is only one major impact.
When the number of product variants increases, the deviation from the standardized process also increases. The high diversity of parts means higher planning effort, more tools, more frequent changeovers and risk of errors. As a result, the overall throughput time increases and due to lower capacity utilization, manufacturing efficiency drops.
As product life cycles are becoming shorter and the rate of new product introduction is high, there is big pressure on development expenses. With a constantly growing product range, regular portfolio reviews are becoming even more important. A complex product portfolio hampers fast detection of unprofitability of offered variants. Furthermore, it leads to higher expenses in the procurement process: as the overall purchasing volumes of input materials are split amongst several variants, volume discounts are less often attainable and supplier handling efforts increase.
The challenge for variant-driven supply chains is to find the trade-off between product variety and the supply chain performance. Product variety can lead to better sales opportunities. This might affect supply chain costs as they are heavily affected by the size and complexity of the product portfolio. To react on variant-driven uncertainty and complexity and ensure high service levels, flexibility in planning and execution needs to be kept as high as possible.
We identified four key pillars to reinvent variant management along the entire supply chain: early customer integration, active portfolio management, holistic product development and design as well as differentiated replenishment and decoupling strategy.
Customers know what they want and what they need. Customer-centric thinking along all business activities is the key to fulfill and adopt to the core customer needs. In the B2B area, these are often triggered by local or country-specific requirements.
The forecast for variant products can be improved by fostering communication and collaboration with customers. An early integration of customer voices also strengthens customer loyalty and satisfaction. Identifying customer segments and analyzing consumption behaviors allow for focused and predictable product development with a reduced risk of failing products and services.
The better the manufacturer understands customer preferences as well as their own capabilities, the better the market and the supply chain view can be integrated into the decision-making processes.
An active portfolio management is aimed at reducing existing complexity, mastering unavoidable complexity, and preventing emerging complexity.
It is of utmost importance to fully understand the existing and planned product portfolio. Thereby product characteristics themselves but also customers come into play. On the product side, important factors are production complexity, contribution margin, position in the product life cycle, demand volumes, as well as variability. Beside these direct factors, there might be strategic reasons to keep or integrate a variant into the product portfolio. An important part of active portfolio management is to use customer and market data as guide for decision making. Thus, it is not only important to gather data and to define corresponding KPIs, but to interpret them correctly to truly understand what is working well and what is less so. That’s why the portfolio analysis should be done based on SKU and customer level. Data-driven portfolio optimization that integrates both sides, the market and supply chain view, is the key to cope with the complexity. Only a holistic approach supports the identification of each variant’s contribution to profit.
Learnings from data-driven portfolio management should be considered as early as possible in the product variant development and design process to ensure flexibility and avoid interfering influences on the supply chain. Integration, combination, and simplification are important factors in the phase of module and variant definitions. Modules are not designed to meet very rare or special requirements but to ease supply chain flexibility while considering the target markets.
The simplification and standardization of parts and components of different product variants can make a major contribution to manufacturing cost reduction. Reducing the number of parts while offering the same variety to the market allows for overall minimization of supply chain risks. If each module consists of as many standard parts as possible, the number of set-ups in production can be reduced. Furthermore, standardized parts and components can be reused for different end products. Thus, aggregated stocks allow for overall safety stock reduction (pooling effect). In addition, economies of scale can be exploited while sourcing parts and components. The idea of standardization should be included into supplier management and procurement. By giving preference to suppliers who are able to deliver standard parts, one can foster supplier relationships and benefit from volume discounts.
Besides segmentation for demand, inventories or commercial/sales prioritization, variants can also be segmented to derive adjusted replenishment strategies. There are two main decision areas with regards to the replenishment and decoupling strategy.
The main task will be deriving the best possible decoupling point between standardized and customized variant production. The well-known rule of thumbs when it comes to variant-driven manufacturing is postponement. The decoupling meaning the actual variant creation should be pushed as much downstream as possible. The delay of differentiation as close to the final demand as possible keeps flexibility in final assembly of demanded variants and reduces lead times between manufacturing and sales. Variants can be created at different levels: at site level, in central or local warehouses or even at the customer.
The chosen strategy depends on the product characteristics and needs to fit to the market requirements and supply chain capabilities.
The second decision is how to create a variant, assemble-to-order (ATO) or assemble-to-stock (ATS).
To define the best set-up for each variant, we conduct a data-driven segmentation that considers the products, the market, the supply chain setup as well as factors like organizational setup and IT-infrastructure together with our customers.
Complexity cannot be avoided completely but with the right approaches it can be managed and controlled. Focusing on the four key pillars mentioned above, leverages a holistic approach to integrate efficient variant-management into all company’s value chain stages, organizational structures, and processes. Boosted efficiency is not only affecting planning quality and reliability but also reveals potential to improve the profit and loss statement. As requirements for and expectations of individual product variants will further increase in future, it is time to challenge the robustness and efficiency of your supply chain setup to cope with variant-driven complexity.
[1] Modeled after: https://www.researchgate.net/publication/274263577_A_Simulation-based_Framework_for_Improving_the_Ecological_and_Economic_Transparency_in_Multi-variant_Production
Modern PLM systems empower businesses to achieve product excellence in fast-paced markets by enhancing collaboration, agility and innovation.
Read how the Campaign Planner & Designer (CPD) helps you to manage supply chain variability.
Explore automated production planning with our Campaign Planner & Designer.
The pharma market trends impact logistics with a shift to smaller, higher-value shipments and new temperature requirements.
© Camelot Management Consultants, Part of Accenture