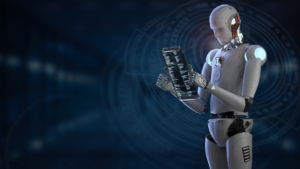
AI-Driven Application & Process Testing: Embracing Agentic Testing
Learn how Agentic AI enables digital transformation, delivering true hyperautomation.
To continue our previous discussion regarding today’s top 10 pharmaceutical supply chain planning requirements, we will further explore some of the potential challenges and solutions companies may encounter within their digital transformation. A successful navigation of these requirements will safeguard the digital roadmap and increase the expected business benefits.
In this article, we will review the first five of the top ten requirements, including:
Each section will give a summary of the challenges driving the requirement, followed by our recommendations for functional solutions and the technical considerations required to implement a digital solution.
To create a finished goods plan, careful harmonization between market requirements and artwork launch strategies is critical to ensure product availability. Within this process, it is of the utmost importance that planners consider artwork dates as they navigate ramp-ups and ramp-downs, approval waiting periods, and hard stops in shipping that can lead to obsolete inventory and risk product availability.
Effective organizational solutions can alleviate the pressure of pharmaceutical artwork planning. Through transparent and coherent cross-functional communication, planners should collaborate with marketing, manufacturing, affiliates, and artwork planning departments. By using artwork strategies for each specific market, they can determine the best dates to make necessary changes without impacting product availability, if market regulations allow it. Such an approach to cross-functional collaboration is essential to ensure that the correct artwork is applied to the appropriate products at the right time.
There are also digital aspects that companies need to consider when designing artwork planning solutions. Incorporating these will determine the complexity of the solution and the supply chain function’s ability to consider artwork changes in planning. These aspects include a Stock Keeping Unit (SKU) strategy to differentiate PPMs (Printed Packaging Materials) in the ERP system, an ERP process to update the Bill of Materials (BOM) to reflect artwork changes in the future, the ability to consider artwork validity dates as constraints for supply and production planning, and the level of automation required to plan artwork ramp-ups and ramp-downs.
Tender management in the pharmaceutical industry involves competing for contracts that secure a confirmed volume over an extended period. Typically, tenders will represent a large volume compared to normal product demand, requiring meticulous planning to ensure continuous product availability and to prevent issues like non-delivery or late fees. During the bidding phase, it is essential to have clear insights into the current confirmed demand, available supply, and available capacity within the supply chain network. This helps in assessing the feasibility of committing to the additional tender volume. This evaluation typically requires planners to develop various scenarios parallel to their active plan until the tender demand is confirmed, accounting for potential outcomes. If the tender is awarded, the plan is integrated into the current live plan, otherwise, it is discarded.
The commercial organization should involve the supply chain planning team in the bidding and evaluation process to ensure an accurate understanding of feasibility. Additionally, intricately connecting tender planning with the Sales and Operations Planning (S&OP) process becomes pivotal. This connection guarantees the proper prioritization and allocation of demand in accordance with the business strategy – especially in scenarios where there might be constraints on capacity.
Effective tender planning in the pharmaceutical industry relies on several critical factors: These include connecting with commercial systems for efficiency, reserving resources based on the probability of winning tenders, and easily comparing scenarios for better decision-making. A high level of automation across end-to-end planning capabilities will optimize resource allocation and enhance responsiveness while integrating financial values ensures the pricing aligns with the company’s goals.
With today’s inherent complexity of pharmaceutical processes and increasing supply chain challenges, there has been growing importance on resource optimization for a smooth production flow and to expedite manufacturing. To support this, companies can implement strategies such as campaigning, product wheels, and sequencing. Different process constraints, like sequence-dependent setup, tool management, or parallel processing, must be considered when determining which planning concepts are appropriate for each respective production process. Depending on a company’s unique needs, planners must consider these constraints and weigh them against potential drawbacks to assess the strategy’s overall advantages.
It is crucial that the supply chain function, operations, and related teams collaboratively identify constraints, such as artwork availability, downtimes, and overutilization. Establishing Sales & Operations Planning (S&OP) and Sales & Operations Execution (S&OE) processes to conduct these conversations will increase the maturity of the planning process. During the S&OP process, teams discuss tactical constraints. During the S&OE process, they develop corrective actions for operational plans to be approved. The detailed scheduling, which is necessary for campaigning and other methods, can be restricted to short- and mid-term horizons according to each horizon’s planning approach.
As part of a digital solution, companies must evaluate the advantages of using a heuristic versus an optimizer, and rough-cut planning versus detailed scheduling respective to the company’s scale and process complexity. Increased levels of automation and integration with operations will impact the complexity of the implementation, but it will increase efficiency, support planning strategies, and optimize the resource network by leveling. Additionally, companies must evaluate the efforts required to update the master data and model complex constraints for a sustainable solution.
The long lead times inherent in Quality Control and Quality Assurance processes significantly impact the product availability. To effectively manage this, it is crucial to carefully factor in these lead times and, if needed, to assess the available capacity to execute these activities. This visibility and consideration in planning enables correct evaluation of product availability and precise prioritization in case of a QA/QC backlog, allowing planners to manage delivery dates and mitigate possible delays proactively.
To cope with the challenges of QA/QC delays operationally, it is important to closely manage the expected release dates during the S&OE process. This allows planners to promptly address supply risks caused by deviations that can potentially impact the product release dates. Strategically, companies should carefully review and consider establishing different types of forward processing methodologies, such as pack-at-risk and ship-at-risk, to parallelize activities and reduce overall product lead times.
While designing a digital solution to consider QA/QC activities in planning, the following factors must be considered and evaluated based on company needs: (1) the modeling efforts of the QA/QC activities versus the gained planning functionalities; (2) the ability and need to model forward processing methodologies in planning; (3) and the level of integration required into the quality execution processes.
Companies are increasingly turning to CMOs to quickly extend their manufacturing capacities and support their supply chains. This brings additional complexity since most of the material flow is not managed directly by the company and requires tight integration with the CMOs. Some aspects of these integrations are an understanding of current inventory levels at the CMOs, an understanding of promise availability dates, and potential disruptions.
It is crucial to establish a well-defined framework with the CMO, covering communication methods, agreed-upon planning assumptions, and commitment timelines. Introducing alignment meetings with the CMO, such as POD (Purpose Outcome Decision) meetings, will enable tighter integration and faster response to disruptions. In these meetings, a designated CMO liaison within the company should facilitate communication between CMOs and internal stakeholders. This will ensure seamless information exchange, including topics such as risks and exceptions in planning cycles, enabling early risk mitigation, enhancing transparency, and integrating seamlessly into the current plan.
When defining a digital solution for CMO planning, the following factors need to be considered:
In this first part of examining the top 10 pharmaceutical supply chain planning requirements, we reviewed five critical areas: Artwork Constraints, Tender Management, Sequencing and Resource Optimization, Quality Assurance/Quality Control (QA/QC) Planning, and Contract Manufacturing Organization (CMO) Integration. Addressing these challenges with effective organizational strategies and digital solutions is essential for optimizing the supply chain nodes (shown in figure 2), ensuring product availability, and enhancing overall business performance.
Camelot’s Life Science Industry Consulting
Authors: Daniel Silva, Lauren Kessler, Rebecca Barr
Learn how Agentic AI enables digital transformation, delivering true hyperautomation.
Reimagine resilience and proactively minimize supply chain risks
This article shall help you to understand how to optimize your inventory positions in a month – or even less.
Modern PLM systems empower businesses to achieve product excellence in fast-paced markets by enhancing collaboration, agility and innovation.
© Camelot Management Consultants, Part of Accenture
Camelot Management Consultants is the brand name through which the member firms Camelot Management Consultants GmbH, Camelot ITLab GmbH and their local subsidiaries operate and deliver their services.