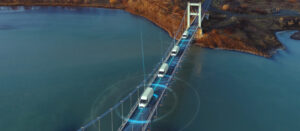
Risk & Resilience in Logistics Network Design
Reimagine resilience and proactively minimize supply chain risks
The semiconductor industry, a cornerstone in the technological revolution, faces a lot of challenges in its supply planning processes. With increasing demand, sophisticated manufacturing processes like wafer fab, wafer test, assembly, and final test with globalized supply chain, semiconductor companies must deal with huge complexities. Such challenges can impact operational efficiency and profitability. In this article, we explore some of the key challenges faced by the semiconductor industry in the supply planning process. We will delve deep into how the SAP Integrated Business Planning (IBP) Time Series-based Supply Planning Optimizer can serve as a transformative solution.
Semiconductor companies must face the inherent volatility of the technology market. Rapid shifts in consumer preferences, emerging technologies, and macroeconomic factors contribute to unpredictable demand patterns. Such fluctuations in demand can lead to either excess inventory resulting in high operating costs, or a stockout situation affecting the service levels.
The semiconductor industry is minted with long lead times in the manufacturing process. Particularly in wafer fabs, which are typically around 2-3 months. This fact, coupled with short product lifecycles at the beginning of a product ramp-up curve paired with unstable yields, are key challenges which need to be considered in a dynamic supply planning.
Semiconductor manufacturing involves complex production processes combined with multi-stage sourcing, including in-house and outsourced manufacturing steps. Disruptions or unplanned bottlenecks at any stage can have cascading effects on the entire supply chain. This leads to capacity losses, increased production costs, and potential delays.
The semiconductor supply chain network is globally located with components sourced from various continents. Geopolitical events, natural disasters, or disruptions in one part of the world can have ripple effects throughout the whole supply chain. Managing and mitigating these risks effectively requires real-time visibility and strategic planning.
All these challenges could not be effectively tackled by heuristics-based or rule-based planning approaches. They require an advanced planning engine like the Optimizer which has the capability to analyze a wide range of data including demand forecast, inventory levels, and production capacities. Based on its analysis, the Optimizer draws conclusion on how effectively all the available resources can be utilized and generates a cost-effective supply plan which is best suited to the business requirements.
Figure 1 shows the main characteristics of planning with the unconstrained heuristic (time-series-based supply planning heuristic), the priority heuristic (time-series-based supply planning finite heuristic), and the SAP IBP Time-series based Supply Planning Optimizer, as well as their positions on a complexity and a solution quality axis.
Before moving ahead with how the SAP IBP Time-series based Supply Planning Optimizer can solve the challenges in the semiconductor industry, let us try to understand what a Supply Planning Optimizer is and how it is different from the other available solutions on the market.
As part of the SAP IBP Response and Supply suite, the SAP IBP Time-series based Supply Planning Optimizer is a supply planning engine that employs a cost based mathematical model. The model considers a wide range of supply chain constraints such as production capacity, transport capacity, handling capacity, safety stock, material availability and many more, to come up with a constrained and cost-optimized plan for procurement, production, and distribution.
The Optimizer is driven by a cost model, which can be configured and tailored to specific business needs such as prioritizing specific customers, prioritizing a particular source of supply, or maintaining inventory at a certain level of supply chain. The Optimizer can be set up to either maximize the profits or to maximize service levels based on the business objectives.
In addition to these, there are several other costs that can be modelled as per the business’ needs. Along with the costs, there are many constraints like maximum or minimum lot sizes, maximum or minimum production or transportation that can also be modelled to fine tune the decision making.
Figure 2 shows the input and output of the Optimizer engine. The inputs are derived by identifying supply chain constraints, setting up cost models based on the business scenarios, and configuring the Optimizer profile to fine tune these results. Considering all these inputs while running iterations, the Optimizer generates an optimized supply plan adhering to the constraints and costs.
To put in the perspective of semiconductor companies, all the challenges described in the first section could be handled well with the Optimizer model just described:
In addition, to mitigate the risks associated with short product lifecycles and potential obsolescence, maximum inventory level for each product can also be configured as constraint for Optimizer. This prevents the optimizer from producing and holding more than the predefined threshold.
In summary, the semiconductor industry’s supply planning challenges demand a sophisticated solution: The SAP IBP Time-series based Supply Planning Optimizer emerges as a transformative answer. Addressing issues that occur due to volatile demand, long lead times, and complex manufacturing processes, the Optimizer provides a dynamic and configurable approach. By categorizing and prioritizing demand signals, prioritizing production sources, and managing lead times strategically, semiconductor companies can achieve a resilient and cost-effective supply plan.
Leveraging the Optimizer’s ability to model costs, constraints, and business rules allows for tailored planning approach, enhancing visibility and prioritizing critical aspects. The SAP IBP Time-series based Supply Planning Optimizer offers semiconductor manufacturers an efficient, responsive, and profitable solution to their supply planning complexities.
Reimagine resilience and proactively minimize supply chain risks
This article shall help you to understand how to optimize your inventory positions in a month – or even less.
Modern PLM systems empower businesses to achieve product excellence in fast-paced markets by enhancing collaboration, agility and innovation.
Read how the Campaign Planner & Designer (CPD) helps you to manage supply chain variability.
© Camelot Management Consultants, Part of Accenture
Camelot Management Consultants is the brand name through which the member firms Camelot Management Consultants GmbH, Camelot ITLab GmbH and their local subsidiaries operate and deliver their services.